Speciality Chemicals Firms Order Rise Amid Covid-19 Pandemic
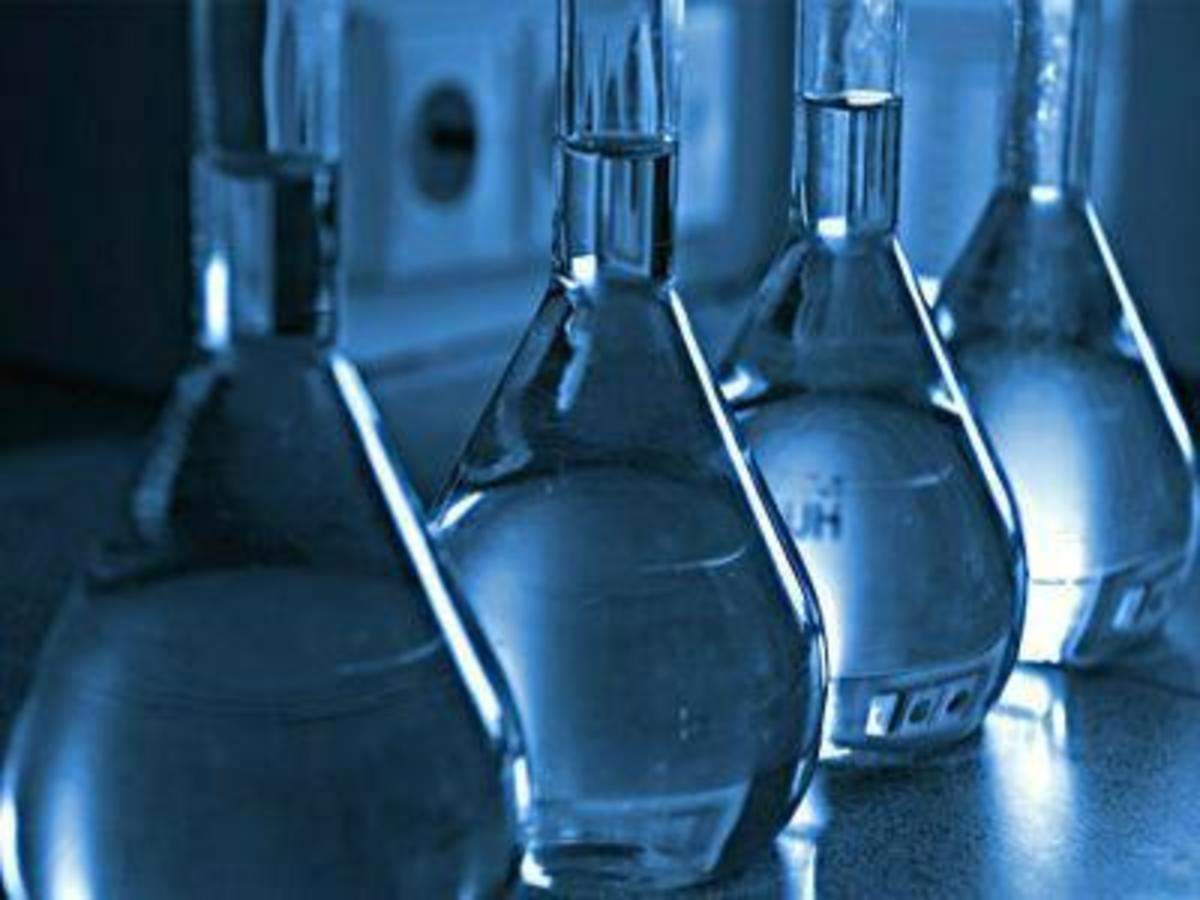
“Specialty chemical manufacturers faced logistics and labour issues when a nationwide lockdown to control the novel coronavirus outbreak froze supply chains. However, one industry is expected to recover more quickly than others. This is due to the fact that the industry continues to function, but at a reduced capacity, as a supplier of chemicals to critical industries such as pharmaceuticals, personal health, and hygiene.”
Since the sector is reliant on exports, analysts and company executives expect output to improve. Furthermore, China's production in this segment is expected to decline, opening up more opportunities for domestic specialty chemical producers. The expected rise in importers looking for an alternative supply chain, particularly in the context of the coronavirus outbreak, is a trigger for specialty chemical players. In this vein, Japan has set aside $2.2 billion to assist its producers in shifting production away from China. Frequent supply disruptions in China (which began with environmental concerns and was later led by Covid 19) and MNCs' excessive reliance on Chinese supplies have already resulted in a number of early innovations in manufacturing shifting to India.
THE OIL, GAS, AND CHEMICAL industries experienced an unexpected turning point in the first quarter of 2020. The combined effects of the COVID-19-related economic downturn and the oil price crash reverberated across these sectors, which were already dealing with difficult long-term trends. The events of early 2020 compounded three of these patterns in particular:
- Growing customer understanding of environmental issues has prompted energy and chemical companies to look into decarbonization technologies, reassess their properties, and diversify away from hydrocarbons where possible.
- Workplace adoption of emerging technology is changing work and the workforce.
- In certain market segments, chemical companies have been experiencing oversupply.
Demand Is Unevenly Distributed Across Segments
Polymers and plastics, adhesives, paints and coatings, lubricants, cleaning products, and many other industries use specialty chemicals in a variety of ways. Any disruption in this industry has repercussions in a number of other industries that depend on specialty chemicals. After the outbreak, there has been an uneven demand for specialty chemicals across various segments. Although demand for specialty chemicals has decreased dramatically in the paints and coatings industry, it has increased or remained steady in the manufacturing of pharmaceuticals, cleaning agents, detergents, flavours and fragrances, and plastics.
The paints and coatings industry has been seriously harmed by a sharp drop in demand in its two main end-use markets, construction and automotive. After the pandemic threat has passed and market conditions have returned to pre-outbreak levels, specialty chemical manufacturers will need to make well-informed strategic adjustments and restructure their businesses to handle this uneven demand scenario.
Manufacturers of Specialty Chemicals are Affected
Specialty chemical producers have had a mixed reaction to the pandemic. Low oil prices lowered raw material costs for some product lines, while Chinese plant closures aided manufacturers in Europe, the United States, and India in filling the gap and increasing order intakes. Supply chain disruptions, on the other hand, have caused procurement issues for a number of manufacturers. Companies that rely on Chinese raw materials face considerable logistical difficulties.
Specialty chemical producers will feel the brunt of the effect in Q1 2021, rather than Q4 2020. Clariant and Evonik, two specialty chemical companies, have already posted lower earnings for the first quarter of 2020. Even after the lockdown in developed economies is lifted, demand is not expected to grow dramatically, so these companies will mostly experience a U-shaped recovery. Once factories reopen and supply chains become more fluid, specialty chemical manufacturers are most likely to meet their current order commitments by the end of 2020. The length of time it takes to recover and the duration of the recovery will be determined by how quickly lockdowns are removed in different parts of the world and how quickly the world will recover.
Trends are accelerating.
A subset of interviewed chemicals CEOs, division executives, and R&D leaders expressed a simple strategy: The majority of financially strong businesses plan to increase their investment in some projects that they see as accelerating and that will improve their competitive position in the future. Since these strategies are linked to structural developments that are expected to accelerate both brands and governments, this approach is likely to yield competitive advantages in the future.
- Remote or digital sales platforms are preferred: Due to social distancing and constraints, more B2B and B2C interactions are taking place across remote or interactive networks and experiences.
- Focus on health and safety: Consumers are demanding that brands and policymakers take safety and precautionary steps.
- Pop-up ecosystems are forming: Value chain disruption is likely to lead to more innovative collaborations.
- Investments in development and the circular economy: Since the outbreak of the pandemic, environmental, social, and governance investments have seen a steady rise in inflows and higher-than-average returns.
- Biocidal and usable materials are in high demand: The COVID-19 pandemic has given biocidal paints, coatings, and surfaces a new lease on life in public spaces including hospitals and schools.
- Visualisation of the workforce: Organizations have already adapted to operating remotely and have started to implement new business models as a result of workforce virtualization.
- Digitalization of key business processes: As a result of social distancing, more people are adopting contactless technology and digital interactions (e.g., advanced analytics, 5G).
On-going Trends in the Chemical and Materials Industry
Continuing Trends
Several main trends in the chemicals and materials space are expected to continue apace, according to comments from industry participants and our own research:
- Chemical output capacity expansion: Global chemical manufacturers and integrated oil and gas players have been forced to continually add new capacity due to rising demand. Owing to the pandemic, however, many capacity-focused capital spending programmes have been postponed.
- Accelerated energy transition: While electricity demand has decreased as a result of government lockdown policies, total renewable generation has remained at pre-crisis levels with low electricity prices, potentially speeding up the electricity system.
- Public desires for sustainable goods: The pandemic have raised awareness of the near link between human and environmental health, resulting in a continued consumer-driven demand for sustainable products.
- Concern for environmental problems in society: Consumer support for reducing carbon emissions is one of the top factors behind the chemical industry's shift to a sustainable, low-carbon future, according to executives.
Sustainable goods are preferred by consumers.
The phase-out of some single-use plastics—bags, straws, and cups—in a number of countries and US states gave a peek into the potential for such measures to disrupt the chemicals industry. It was evident in this sense that the implementation of sustainable practises was expected to accelerate. What is perhaps surprising is business executives' unwavering support for environmental programmes, even during periods of economic hardship brought on by the pandemic. Although it is clear that the dedication to sustainability and climate change issues is driving this view, there is also a potential US$120 billion market opportunity.
Closed-loop recycling, in which polymers are chemically reduced to their original monomer forms so that they can be recycled or repolymerized and remade into new plastic products, is likely to be at the forefront of such sustainable practises. Furthermore, chemical producers have the option of using products that are more easily recyclable or bio-based. Consumer behaviour must move toward accepting and utilising such materials, even at a higher price point, for this trend to be sustainable.
The increased emphasis on sustainability has been perhaps the most counterintuitive of all the accelerating developments. Although COVID-19 has clearly reminded consumers of the value proposition for plastics used to protect people, food, and health-care items, the commitment to green and blue hydrogen (green—produced by renewable energy electrolysis; blue—with carbon capture) and chemical recycling appears to be as strong as ever. According to one report, more than US$300 million has been invested in plastics recycling start-ups only this year. This is in addition to the numerous internal projects focusing on sustainability that are ongoing in corporations' R&D departments.
The consequences of future scenarios
The conversations with executives and secondary analysis were used to create scenarios that took into account the pandemic's long-term effects and the advent of a new status quo. But what are scenarios, and why are they so essential in planning?
The events surrounding the emergence and spread of COVID-19 have highlighted the difficulty of making predictions, especially about the future, as societies and businesses have had to undo plans that were well-crafted but not flexible enough to meet rapidly changing circumstances. Scenario planning recognises that accurate forecasting of the future is difficult. Focusing on key uncertainties and developing scenarios that can be used for business planning around these uncertainties is feasible. In industry, it's a fair deal to trade unrealistic precision for robustness and resilience.
Major Market Highlights:
- Aarti Industries in India accounts for 75% of the global market and is ranked in the range of first to the fourth position covering a market share of 25-40% respectively. Ranked third in chlorination, fourth in nitration and second in Ammonolysis and hydrogenation.
- Axalta, a leading global supplier of liquid and powder coatings, reported in November 2020 that it had completed the acquisition of Capital Paints LLC, a thermosetting powder coatings manufacturer based in the United Arab Emirates.
- PPG acquired Dexmet Corporation, a manufacturer of specialty materials for surfaces in aerospace, automotive, and industrial applications.
- ArrMaz, a world pioneer in specialty surfactants for crop nutrition, mining, and infrastructure markets, was acquired by Arkema.
Conclusion: Moving Forward
Most chemical companies' initial reaction has been very positive. The chemical industry's biggest players have thrown their support behind people suffering from COVID-19 by donating. They also assist their workers by providing health benefits, implementing COVID-19 prevention initiatives, and providing rational help. Disinfectants, masks, antiseptics, gloves, personal security devices, and other market segments have seen huge sales as a result of the outbreak. This could be a one-time business impact, but it could also start a long-term trend. Globally, demand for packaging materials is rising as more people stay indoors and focus on packaged food delivered to their homes.
Chemical producers in a number of countries are reporting success in their attempts to keep their companies afloat amid significant losses due to the pandemic. Companies with operations in China are resuming operations, and others who rely on raw materials from China are expecting to obtain the materials as supply chains are rerouted.
Chemical firms, like many other manufacturers, are vulnerable to the damage caused by the COVID-19 outbreak on multiple levels. In the near future, they will have to balance keeping their employees and their families secure while continuing to operate as normally as possible.
Feedstock price instability, supply chain and logistics problems, and volatile consumer demand can all be challenges for commodity chemicals companies. In addition, the industry will need to find alternatives to its dependence on China-based suppliers.
Looking ahead to the virus's containment and eventual economic recovery, chemical companies should consider how the industry could recover, and what measures they should take now to place themselves as best they can in a post-COVID-19 environment.