Industry 4.0 - Transforming the Chemical Industry
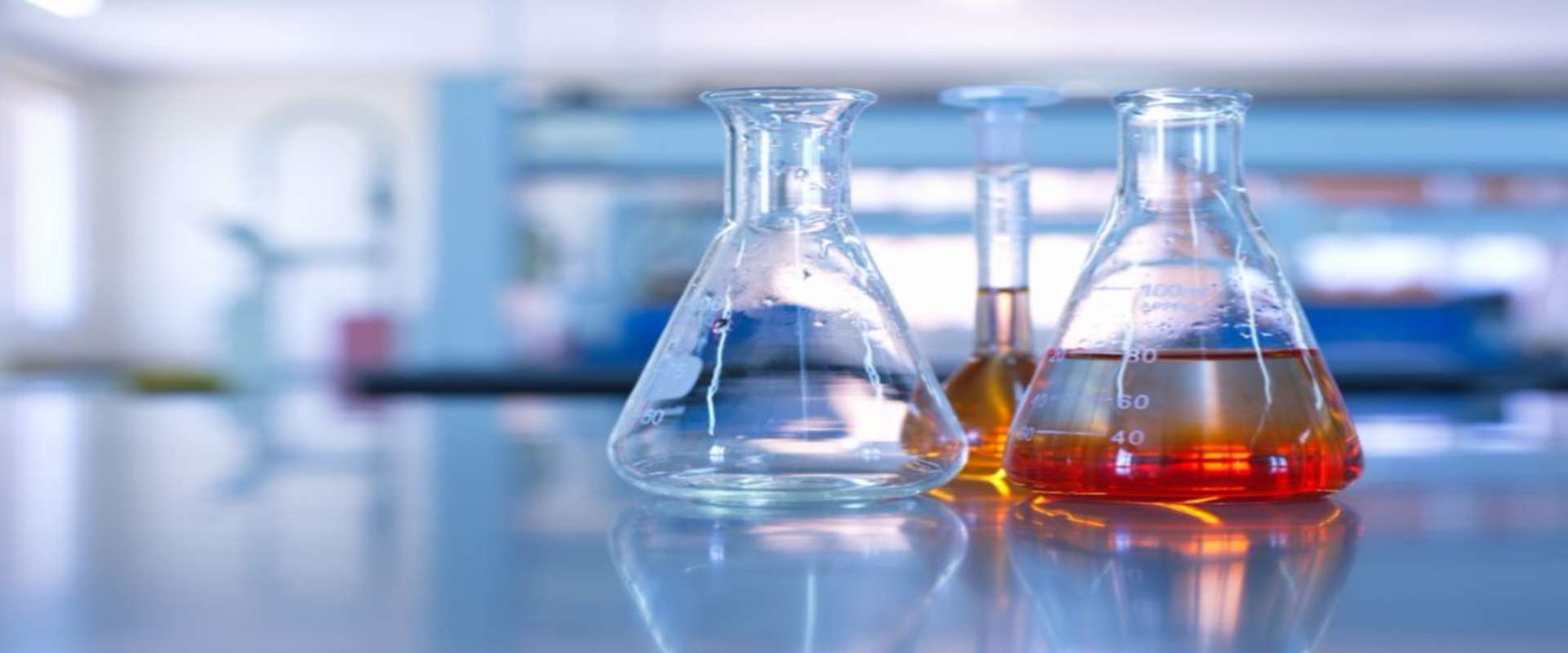
“The chemicals sector, which is the backbone of many end-market industries, could be transformed by Industry 4.0, which blends digital and physical advanced technology. These technologies enable "smart" supply chains and factories, as well as new business models, through their dual fields of company operations and growth.”
Almost every produced product is influenced by the chemicals sector in some way. Petroleum and natural gas are transformed into intermediate materials, which are then transformed into items we use every day. The worldwide chemicals industry, which employs more than 20 million people and generates $5 trillion in annual sales, is the backbone of numerous end-market industries such as agricultural, automotive, construction, and medicines. As a result, changes in the chemicals business are likely to have an impact on a variety of other businesses.
What does Industry 4.0 have in store for chemicals?
Organizations focused on business operations can leverage Industry 4.0 technologies to enhance productivity and decrease risk, while those focused on growth can utilise Industry 4.0 to produce incremental revenue or entirely new revenue streams.
Because of the large amount of historical sensor data acquired by chemicals businesses over the years, the initial impetus of Industry 4.0 in the chemicals industry is predominantly at the level of business operations. Business growth applications have the potential to be equally, if not more, transformative in the long run, but they take time to build.
Various smart manufacturing strategies, such as predictive asset management, process control, and production simulations, can boost the productivity of chemical plants.
Productivity and risk management are two important aspects of improving corporate operations.
Various smart manufacturing strategies, such as predictive asset management, process control, and production simulations, can boost the productivity of chemical plants. Risk reduction, on the other hand, necessitates managing supply chains and internal processes in order to respond to changing client demand while also improving safety and quality.
Asset management with foresight
The chemicals business is known for its high asset concentration. As a result, sophisticated IT/OT technologies can assist businesses in reducing maintenance costs and increasing asset efficiency by using predictive or digital maintenance. Advanced analytics systems can spot trends in data received from sensors on important equipment such as turbines, compressors, and extruders in order to detect and diagnose possible malfunctions. Smart equipment can then provide plant operators messages regarding any needed maintenance, prospective malfunctions, and parts ordering and delivery timelines.
Manufacturers may be able to transition from scheduled or reactive repairs to predictive maintenance as a result of this. Data from similar equipment installed at other locations can also be collected, compared, and used for predictive maintenance, performance optimization, and facility design.
Control and management of processes
Previously, petrochemicals businesses' control rooms had analogue controllers along the walls, and operators went around the room manually examining readings to determine plant operations and conditions. Data is collected through networked systems and provided to operators digitally in modern control rooms, eliminating the need for manual reviews and saving operators time and effort. 11 However, digitization is merely the first phase.
Real-time analytics and automated control actions are examples of Industry 4.0 technologies that integrate the digital and physical worlds together to support prediction, alerts, and prescriptive reactions. As a result, batch consistency and quality can be better controlled.
However, digitization is merely the first stage. Real-time analytics and automated control actions are examples of Industry 4.0 technologies that integrate the digital and physical worlds together to support prediction, alerts, and prescriptive reactions.
Management of energy
The cost of energy plays a considerable role in the production expenses of a chemical plant. Multiple activities and their interconnections are common in a typical plant, making it challenging for operators to choose the best operating conditions. Borealis, for example, employs data mining and modelling to establish dynamic goal values for a plant's energy consumption, taking into account aspects like the plant's current circumstances, outside temperatures, fouling of the systems, catalyst ageing, and so on.
The chemical industry is highly automated, and most plants use standard variables like temperature, flows, tank levels, and pressures to determine the best operating conditions. Industry 4.0 technologies like soft or virtual software sensors, on the other hand, can supplement these data points with extra information and enable control of nonstandard process variables to increase energy efficiency.
Management of safety
Chemical firms must secure the safety of their employees, supply chain partners, and customers throughout the product life cycle, from manufacture through storage, transportation, and ultimate usage, due to the delicate nature of their products.
While traditional safety measures entail sampling and monitoring, linked technologies can assist businesses in continuously monitoring products, by-products, and any waste generated. Smart (piezoelectric composite) paints, for example, can detect mechanical vibrations or other changes in a chemical tank, such as corrosion or cracks, and alert the operators, lowering production hazards.
Visibility of the supply chain
Chemical firms primarily operate on a business-to-business basis, selling products that are then utilised by their customers to develop new ones. Customers may request that products be delivered within a specified temperature or pressure range so that they can be used in later manufacturing operations. Many organisations in the upstream and downstream value chain employ connected instruments like Ovinto satellite monitoring devices on railcars to monitor chemicals during transportation, which is a critical time for monitoring and controlling conditions.
The device has a GPS to track the railcar's location, and several sensors analyse the physical qualities of the chemicals as well as the railcar's condition using data such as shock impacts. The data is collected by satellites in low Earth orbit, which ensures continuous communication.
Forecasting demand
Demand forecasting and responsive scheduling can help chemical industries optimise capacity. BASF, for example, is using predictive analytics to forecast demand by merging historical data with economic data. External factors like seasonal effects, macroeconomic data for customer industries at national and regional levels, regulatory changes, and internal factors like BASF's strategies—expansion, mergers and acquisitions, divestitures, and other transactions—are all taken into account by the forecasting model. BASF can plan and alter its plant operations as demand changes using the forecasting model.
Material selection using advanced analytics
Chemical businesses can employ advanced analytics to generate new "physical" materials using digital data. Lower data storage costs, high-performance computing (HPC), and advanced analytics all aid in the creation of databases that store information on available materials and their properties, as well as present new material combinations with desired properties, resulting in material genomics advancements. Chemical businesses might potentially digitise the material-selection process by moving away from trial and error and toward modelled outcomes.
Existing revenue streams will be supplemented by data services.
Chemical firms can use data services to supplement their present product income, thanks to information and networked systems. Monsanto, for example, has a “Climate Basic” app that gives farmers real-time data from satellites on temperature, weather, and soil conditions, as well as forecasts for the next few days, as well as advice on appropriate water levels and fertilisers based on the data obtained in the field.
There are also software applications that assist farmers in detecting and diagnosing plant illnesses. The farmer can take a photograph of the diseased plant and upload it to an analytical model. The model compares the sick portion of the leaf to photos of diseased plants saved on a connected database. Once the model has found a match, it makes therapy recommendations. The image could also be forwarded to a laboratory and evaluated by pathologists for validation of computerised advice.
By forward-integrating into customers' activities, new revenue models can be created.
Chemical firms have the chance to integrate their collaborative knowledge into the operations of their customers. Traditional manufacturers made water-treatment suggestions to their customers based on site visits and their understanding of materials and assets, in addition to providing water-treatment chemicals.
Chemical companies can have direct visibility into and interaction with their customers' operations using Industry 4.0 connectivity, monitoring, and analytics, and can provide real-time recommendations to optimise operations and improve the design of water-treatment facilities, allowing them to create a new business model for themselves. Ecolab, for example, is a company that delivers water purification as a service. In addition to providing water-treatment chemicals, the company leverages advanced analytics to provide real-time monitoring of customers' operations and assets, as well as advice on water use, reuse, and recycling.
Major Market Highlights:
- Solvay has stated that the capacity of its hydrogen peroxide plant in Jemeppe-sur-Sambre (Belgium) will be increased, allowing for increased H2O2 production. The company also intends to enhance the capacity of its plants in Bernburg (Germany) and Voikkaa (Finland) (Finland). These expenditures are in response to increased product demand in Europe, both for existing and new applications.
- Kanto Chemical Co., Inc. committed around USD 63.7 million in expanding its production facilities in Taiwan to suit the growing demand of key local semiconductor clients. The annual output of semiconductor products will expand from 120,000 to 200,000 tonnes at this facility.
- Cabot Microelectronics purchased KMG Chemicals (US) and became the North American region's biggest chemical distributor of semiconductor consumable materials. Cabot's existing portfolio will be supplemented by this acquisition, which will expand customer touchpoints with leading semiconductor manufacturers.
Conclusion: Industry 4.0 will bring several opportunities in the chemical industry
As firms move away from the pay-by-the-ton revenue model and focus on providing value-added products and services to their customers, Industry 4.0 will certainly have an impact on how they run and expand their operations. The decisions firms make today, as well as the activities they commit to in the coming years, will determine how quickly and successfully they perform.
Chemical firms can plan their Industry 4.0 journey and identify ways to connect their digital and physical assets across different stages of the value chain if they have a strong grasp of their strategic imperatives.