Engineering Plastic and PP Compound Goods - Growing Application in Automotive and Consumer Sector
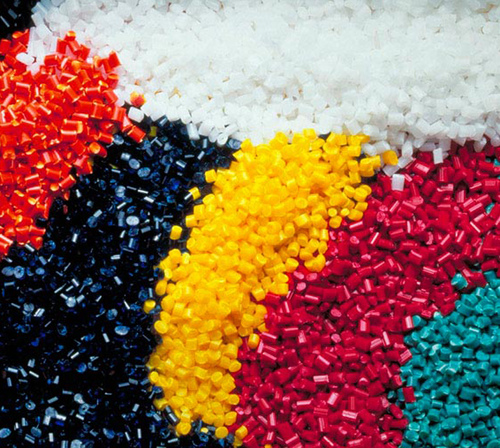
“After packaging and building & construction, the automotive industry is the third largest consumer of polymers. As a result, shifts in material use can have a significant impact on polymer demand and polymer producers' financial results. We clarify how material use patterns are likely to change in this article, as well as the effects electric vehicles would have on polymer use.”
With stricter regulations and evolving customer preferences driving demand for more affordable, lightweight, and fuel-efficient vehicles, the role of plastic in the design and manufacture of automotive vehicles has never been more critical. Owing to - fuel prices and tighter environmental regulations, fuel efficiency has become one of the most critical features in automotive vehicle design. This, combined with strong demand for automobiles and growing disposable income in emerging economies, will continue to drive plastics demand in the automotive industry.
Several metals, plastics, and composites have been developed for use in the automotive industry as a part of the lightweight revolution. The introduction of new materials has created a highly competitive environment in which manufacturers compete to offer the best-fitting solution to their customers.
Today's content suppliers are focused not only on the lightweight design of their products, but also on their cost competitiveness and efficiency.
PP compound has cemented its position in the automotive plastics industry due to its cost-effectiveness and superior material characteristics. PP compound is the most widely used plastic in the automotive industry, with applications in the interior, exterior, engine, and transmission. TPO and TPV PP compound, mineral-filled PP compound, and glass-reinforced PP compound are the three main types of PP compound used in the automotive industry.
Polypropylene (PP) compounds have largely replaced engineering plastics and metals in automotive components, resulting in substantial weight reduction and cost savings. PP compounds are inexpensive but have excellent mechanical and moldability properties.
More than half of the plastics used in a car come from these substances. In a number of lower-end automotive applications, PP compounds have succeeded in replacing ABS. This type of replacement is also anticipated in places like centre consoles, door panels, and side pillars. PC/ABS is a highly impact-resistant polymer used in bumpers, but it is losing ground to TPOs, which are a more cost-effective alternative to PC/ABS. In car overhead consoles, LFT-PP also replaces PC/ABS. The use of virgin PP in the automotive industry is limited due to its poor impact and aesthetic efficiency. Surge tanks, battery cases, covers, and door liners are all popular uses for virgin PP in the automotive industry. The demand for virgin PP in the automotive industry is linked to the growing demand for PP compound in the industry. PP compound is threatening to replace direct application of virgin PP in the automotive industry.
Impact of Electric Vehicles on Polymer Consumption
When evaluating the automotive outlook and the resulting polymer market, the introduction and rapid growth of electrically driven road vehicles has become a key issue to consider. Although the global number of electric vehicles (EVs) remains low, vehicle fleet electrification has gained traction in recent years, aided by regulatory incentives, shifting market perceptions, and the auto industry's production of a large number of affordable electric models.
Despite the shift toward electric vehicles, internal combustion engines (ICE) will continue to account for a large portion of the automotive fleet, with fuel efficiency driving polymer innovation. The architecture of an electric vehicle is similar to that of a conventional ICE vehicle, with the key difference being the design and materials used under the hood. Electric vehicles, on the other hand, would be devoid of a fuel system, pump, tanks, and connecting cables, among other things. Polycarbonate (PC) consumption is expected to rise at a faster pace as the demand for electric vehicles grows, as PC would be used in sensors and LEDs in the automobile. As manufacturers strive to reduce costs and weight, polymer components in engine transmissions will become more popular. However, the industry's focus on light weighting, which results in smaller and lighter materials, will offset the consumption of engineered polymers.
HPP in Consumer Products
PET is a thermoplastic polymer that is mechanically solid, shatterproof, unreactive, translucent, lightweight, and reasonably priced. Microorganisms and biodegradation are also immune to it. Regulatory bodies all over the world have given it their approval for food touch applications. PET bottles and cans are used all over the world for food and beverage packaging.
PET bottles for beverages such as soft drinks, fruit juices, and water are the most well-known PET packaging application among the general public. Many other foodstuffs, such as salad dressings, butter, margarine, and cooking oils, are packaged in PET bottles and jars. Cosmetics, personal care goods, over-the-counter medications, dishwashing and laundry detergents, household cleaning solutions, and a variety of other products are all packaged in PET bottles and jars.
PP is a nonpolar (hydrocarbon) thermoplastic polymer that is inexpensive, sturdy, impact-resistant, and lightweight. It can withstand a variety of chemicals. It can withstand a wide range of temperatures, allowing PP packaging to be used in both microwave and freezer applications without losing its integrity.
Many foodstuffs and other non-durable products are packaged in rigid PP containers. Packaging articles such as rigid PP bottles, jars, pots, and bottle tops are made using injection moulding, thermoforming, and blow moulding. Many liquids, powdered, or solid non-durable products, including foodstuffs and both over-the-counter and prescription medications, can be packaged in injection moulded PP bottles. Its major rivals for use in bottles for non-durable products are PET (discussed above, the leader in soft drink bottles) and HDPE (discussed below, the leader in milk bottles).
High Performance Plastics (HPP)
Because of their superior mechanical properties, chemical and/or heat stability, high performance plastics meet higher specifications than regular and engineering plastics. High-performance plastics are also widely used in the automotive industry. The materials mentioned below make up nearly 70% of the total high-performance plastics used in a car and are used for automotive parts and components.
Polypropylene (PP): At very high temperatures, polypropylene has excellent chemical and electrical resistance. It's semi-rigid, transparent, and comes with an integral hinge. PP is a lightweight material that is commonly used as a thermal insulator.
Polymer Demand Patterns Have Changed
In recent years, an increase in the consumption of polypropylene (PP) and polyurethane (PU) has been partly offset by a decrease in the consumption of engineering plastics, with PP and PU accounting for roughly half of total plastic consumption in vehicles. Due to the lower demand for engineering plastics in under-the-hood applications for electric vehicles, where high temperature resistance of engineering polymers is not needed to the same extent as with internal combustion engines, consumption of engineering plastics is expected to decline. Instead, battery brackets and housings in electric vehicles will be made of polyamides.
ABS use is expected to decline as improved polystyrene and PP composites continue to replace ABS in decorative interior pieces, which has historically been dominated by ABS due to the material's gloss, especially in the United States. The high cost of ABS has aided in the replacement of lower-cost polypropylene. ABS consumption for the interior will rise in some high-end vehicles, as customers demand a higher-quality design.
Polymer Producers' Implications
Overall, polymer use in the automotive industry is expected to increase. The rate of growth will be determined by the type of plastic, applications in vehicles, interpolymer substitution, and recycling efforts in various regions. With the introduction of electric vehicles, demand for plastics such as PP, PA, PC, and PE is expected to rise, while demand for engineering plastics is expected to fall. Engineering plastics emerge as "losers," as most of these polymers' high temperature performance isn't needed for electric battery components, fuel systems, or other ICE parts.
Sustainable Mobility
Engineered plastics are quickly becoming the way of the future for two industries: chemical and automotive, as environmental issues impact both. This pose both a challenge and an opportunity for both companies to investigate the recyclability of the materials used. As a result, chemical firms are working to innovate with content producers, components suppliers, and distributors in order to help the automotive industry achieve greater sustainability. As a result, the automotive plastic manufacturing and recycling systems are currently undergoing changes.
Chemical companies have produced bio-sourced and recyclable products to reduce plastic's environmental footprint, according to various sources. Unlike traditional plastics, which are manufactured from petroleum, a bioplastic is a material made from renewable biomass sources. Bioplastics are made from renewable resources, mostly sugar cane starch, but also rice, potatoes, beets, and oil polymers. Improvements in recycling processes have also encouraged producers to use high-performance materials. Sorting, cleaning, shredding, labelling & classification, and extrusion into final part or product are all steps in the recycling process for plastics.
Major Market Highlights:
- In April 2018, BASF launched a new Ultroson production line in Korea. This new production unit has increased the company's annual capacity of polyarylsulfone to 6,000 metric tonnes, allowing it to meet increasing global demand for high-performance thermoplastics in the automotive and electronics industries.
- Celanese began a POM development expansion programme in April 2018. By 2020, Phase 1 of the debottlenecking project should be completed. This debottlenecking would enable the company to meet the rising demand for specialty polymers while still supporting the company's expanding customer base.
- Covestro (Germany) started two new polycarbonate resin production lines in Shanghai, China, in October 2017. The organisation aims to become the world's largest manufacturer of polycarbonate resins by increasing production capacity from 200,000 to 400,000 metric tonnes per year.
- Solvay (Belgium) increased its sulfone polymer production capacity in India and the United States in October 2017 to meet rising demand from the medical and water treatment industries. The company's role in sulfone polymer manufacturing has improved as a result of this expansion, and the company will benefit from the booming demand from the fast-growing water purification and healthcare industries.
Conclusion: Changing Landscape
Engineering plastics have a promising future. The industries supported by these plastics, as well as many others that use conventional materials like metals, glass, and ceramics, will look to the advantages of engineering polymers to help them solve the challenges of spiralling costs. The global economy will continue to have an impact on technological developments. Although not impossible, commercialization of new engineering polymers based on a new monomer is doubtful. Rather, molecular shuffling with existing monomers, blend operation, and processing improvements will be the main focus. Commercialization of aliphatic polyketones and SPS, both of which use commodity monomers, are good examples.
According to numerous research studies, Asia-Pacific was the most important region in 2016, accounting for roughly half of overall market share. The shift in manufacturing to Asia-Pacific emerging economies, especially China, India, Thailand, Vietnam, and Indonesia, is expected to boost industry growth. According to industry studies, an expanding manufacturing base and increased investments in advanced technology for vehicular production are expected to usher in a new age of automobiles, positively affecting the market, and factors such as fuel efficiency have fueled global demand for sustainable plastics.
With plastic playing such an important role in the development of today's light-weight, fuel-efficient cars, it's critical that automakers work together with chemical manufacturers to solve both performance and sustainability issues in order to stay competitive and prosperous.