Robotics and Automation: How Manufacturing Would Look in The Next Decade?
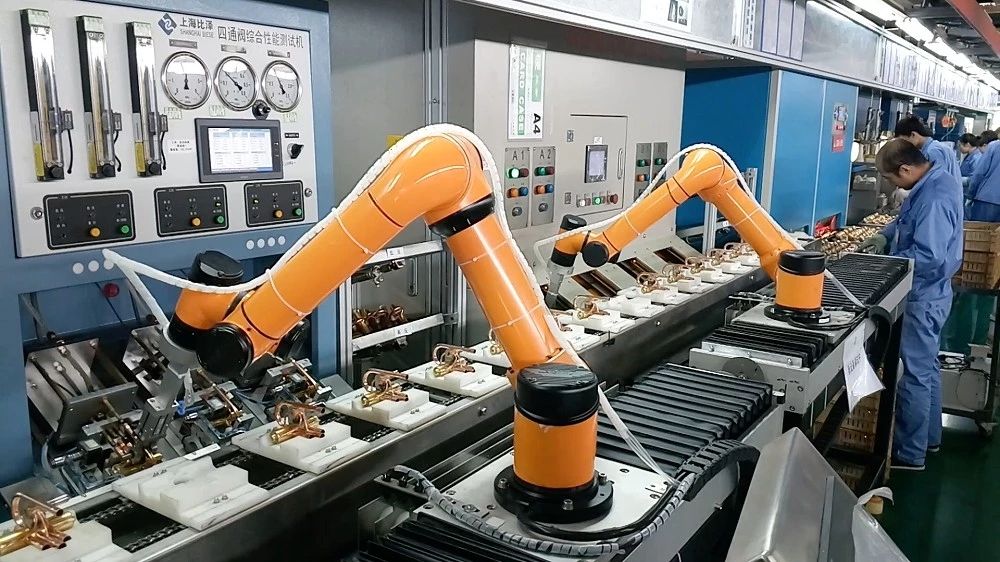
Robotic Automation has made its way into many different fields of manufacturing. Robots perform tasks including welding, assembling, packaging, handling raw materials, and package packing. Robotic automation is being used by an increasing number of manufacturers for a wider range of applications.
Late adopters, who stand to benefit greatly from automation, are seeking answers to the following questions: Are robots too costly for our company? Is our company too small to profit from robotics? Is it difficult to programme and control robots? Would humans lose their jobs as a result of robotics? The short answer is no.
Many different types and sizes of manufacturing companies will benefit from robotic automation.
Here’s why manufacturing enterprises will benefit from robotic automation:
Robotics help you save money and time
In the early 1960s, robots were first used in manufacturing. They've come a long way since then. In comparison to previous decades, robots can now be deployed in less time and at a lower cost. Prices have dropped sharply as a result of increased sales. Robots come with built-in state-of-the-art equipment, quality upgrades, and controlled safety requirements, all of which lead to lower labour costs and less unscheduled downtime. Robots can also work around the clock, increasing production while reducing downtime.
Robots take on additional responsibilities.
These factors are currently assisting in the implementation of robots in the types of applications where they already excel: routine, high-volume development activities. If the cost and complexity of automating tasks with robots decreases, it's possible that businesses that still use them will use them even more. However, we foresee a more fundamental shift in the types of tasks for which robots are both technically and economically feasible in the next five to ten years.
Robotics Can Be Scaled
Robots are used in high-volume, high-production environments, but they can also be scaled down for use in small businesses. In low- to medium-volume manufacturing settings, modern robots may be used. They can now be easily configured and set up for new tasks thanks to recent developments. They can be used in a variety of manufacturing environments thanks to their mobile bases.
Programming Robots Is Easy
To teach robots, one no longer needs to know complex programming languages. There are two simple ways to teach modern robots. The first approach, offline programming, allows a user to model an entire cell, or work area, and create a task's movement sequence.
A teach pendant is the second method for teaching robots. The robot is simply directed through a series of steps by a programmer or engineer. The instructions are stored after some fine-tuning. The robot checks for collisions with objects or humans by slowly running through the software. The robot can now run at full speed after many good test runs.
Robotics Create More Jobs
Because they couldn't compete with low-cost foreign labour, many manufacturers have had to send jobs offshore. Manufacturing can now compete more effectively thanks to robotic automation, which has resulted in the creation of more employment in robotics and related fields.
All of the following skills are required: programming, engineering, end-effector design, operators, data analysts, robot manufacturing, and systems integration. Humans are required to assist in the maintenance of the machines. Robotics allow manufacturers to reduce costs and bring employment back to the United States, resulting in more jobs for Americans. Workers are also protected from having to perform tedious, mundane, and dangerous activities that could jeopardise their ability to function by using robots.
“The Coronavirus is changing the way we work and sparking new manufacturing patterns in this new social distancing age.”
Robots can play a significant role in helping businesses recover in the post-COVID world as we move toward a new standard. Integrators, Original Equipment Manufacturers (OEMs), end-users, and manufacturers are among the key industry segments impacted by COVID-19, according to three automation experts.
The pandemic has posed several questions, including how to minimise “touches” of goods and packaging, how to increase social distance, and how to keep plants running while people are forced to stay at home.
In the future, advances in grippers could aid robotics in reducing touches in manufacturing, warehousing, and logistics. Collaborative robots and mobile robots appear to be particularly well-suited to assist in the creation of social distance. If we have a return to "stay at home" requirements during the next outbreak of this epidemic or in a potential pandemic, adding more robots to manufacturing and logistics operations will help businesses stay up and running or be more profitable.
How would these segments look like after COVID? And, if so, how would the transformation look?
The change to a post-COVID status is likely to see some reduction in spend and manufacturing volume before returning to more usual levels, focusing on the critical industries and the suppliers that support this market. In general, all business segments will need to ensure that their operations are in top shape to respond to a new increase in demand later in 2021.
Covid-19 has strained the supply of human labour to the breaking point, making it nearly impossible for food producers and processors to keep up with production demands, in addition to macro trends such as population growth and ageing, workforce upskilling, and government focus on food safety modernization. These circumstances present opportunities for automation technology manufacturers and system builders. In a nutshell, we are in the midst of the next great automation revolution!
Major Highlights of the Market
- The robotics industry's main trend, especially for machines used in manufacturing and inspection, is that demand is increasing. In 2019, the demand grew significantly, with orders for new robots pouring in throughout the year, resulting in $1.3 billion in orders in only the third quarter.
- As the underlying technology advances, the market for fast, accurate, and dependable robotic automation is likely to rise even further. Manufacturing and inspection processes are still looking for ways to change, which means there's a lot of room for expansion and development. So much so that industry experts expect that by 2024, robotics will be worth more than $40 billion globally.
- The Japanese robotics maker FANUC has been operating a “lights-out” factory since 2001, where robots build other robots completely unsupervised for nearly a month at a time.
Machining, production, and assembly are all areas where Automation excels
The first occupations to be automated are those that are dirty, monotonous, and unsafe. Many human workers in the mass-production assembly line have already been displaced by automation. Cyber-physical systems like industrial robotics and 3D printing are increasingly popular in modern factory. Along with humans, robots have become less expensive, more reliable, safer, and more popular.
Consumer preferences have broadened as well, and manufacturers are scrambling to meet rising demands for customization and variety.
Industry 4.0 visions include a fully autonomous factory where networked machines and products interact through IoT technology to not only test and assemble a particular set of products, but also iterate on them based on customer input and predictive data.
AN INCREASE IN THE USE OF ARTIFICIAL INTELLIGENCE IN ROBOTICS
Artificial Intelligence (AI) is a pivotal advancement for almost every industry right now, but it holds special promise for robotics and automation. Though AI researchers still have a lot of questions and problems to solve, AI is being used in limited ways to provide insights into automated manufacturing processes using sophisticated machine learning. This combination of artificial intelligence and advanced robotic systems can help companies find key areas for improvement.
Whatever the future holds for manufacturing and inspection robotics, Pukka Partners can be counted on to deliver outstanding results.
Conclusion: “Now or Never” is what we say about Automation and Robotics in Manufacturing Industry
In many sectors, industrial robots have played an important role in manufacturing. It all began in the automobile industry. From welding to press tending, assembly, painting, cutting, and material handling, industrial robotics increased productivity in every field, as evidenced by the industry's short production period. Robots perform complex and elaborate application for the computer industry, they are known to perform with precision and speed in the assembly process.
Manufacturers are increasingly turning to robotic automation to cut costs, improve efficiency, and stay competitive. Return on investment can equal growth, which not only boosts profits but also creates employment and saves money for customers.
It appears that a robot revolution will occur in the coming years. It does not imply work extinction, but rather a change in the employment environment. It will almost certainly result in the emergence of new talents, markets, and competition. A potential human-robot partnership that will form many sectors and change the global economy. We must embrace and adapt to the imminent transition that robots will bring to our work as they become more intelligent and flexible.