Next-Gen Technologies Disrupting the Smart Manufacturing
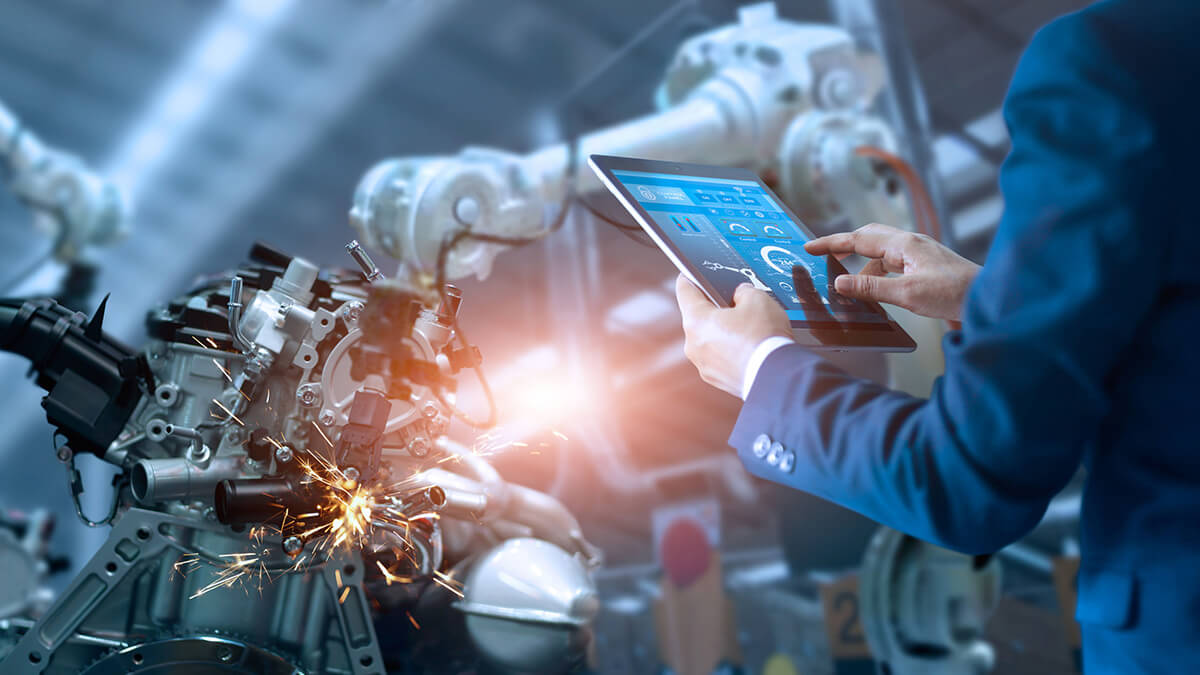
According to a report, companies that fully exploit the innovations and advancements at the heart of the Fourth Industrial Revolution will have a significant advantage in navigating four long-term shifts that are critical to managing unprecedented disruption in the global manufacturing industry. With recent global events, particularly the COVID-19 pandemic, causing significant disruptions on a scale unprecedented in modern history, there have been calls for a "great reset" across all sectors of the global economy: a decisive set of actions that will not only deliver value to businesses, but will also benefit society as a whole. The way prominent corporations have responded to supply chain shocks that have revealed operational vulnerabilities exemplifies this. These businesses have taken advantage of the crisis to implement technological advancements and embrace new ways of working, allowing them to adjust swiftly during periods of upheaval while remaining viable and functioning.
Big Data/Internet of Things (IoT)
Voice-activated speakers, home automation, video doorbells, intelligent thermostats, and smart locks were among the first IoT products to revolutionize the consumer market. With connected machine shops and smart manufacturing, IoT is already making its way onto the shop floor. IoT enables you to keep track of machines by collecting and analyzing specific machine data to detect trends and pinpoint any performance issues. You can adopt improvements and optimize procedures more quickly if you use the data you've acquired. You may use IoT to communicate with CNC machines in a variety of ways, such as scheduling maintenance or receiving messages from the machine when it detects a problem, such as a tool that needs sharpening or odd temperatures or vibrations.
Robotics
The employment of robots for automation is not a new notion in manufacturing, but incorporating linked collaborative robots, or cobots, will transform the way the shop floor operates. Cobots are robots that are designed to work in close quarters or interact with humans in a shared environment. They excel at pre-programmed activities and can be used to automate repetitive or inefficient processes such as transporting heavy parts, machine feeding, placing finished parts in a collection bin, and tool replacement. The machinists are freed up to focus on more demanding projects by having the cobots do the repetitive, mundane chores.
Machine Learning and Artificial Intelligence
Manufacturers are using artificial intelligence (AI) and machine learning algorithms and applications to acquire useful data and make judgments about how to improve production efficiency, quality control, and employee safety. These technologies can assist remove manufacturing bottlenecks, enable smooth inventory management, and allow for real-time process improvement. AI and machine learning will cut labor costs, waste, optimize cycle times, and boost efficiencies on the shop floor and in the office in the long run.
Hybrid and additive manufacturing
Although additive manufacturing (AM) has existed since the 1980s, it has only lately started to make an impact on the machining sector. AM creates three-dimensional sculptures by layering materials such as metal, plastic, and concrete.
The one disadvantage of AM is that the 3D produced object requires a lot of post-processing and finishing to match the tolerances. Hybrid manufacturing can help in this situation. Within the same machine, hybrid manufacturing mixes additive and subtractive manufacturing. The advantage of hybrid machines is that they can create and complete a part in one operation, which reduces errors. It is not necessary for a part to leave one machine to be reset on another.
Embedded Meteorology
Traditional quality control procedures can be time-consuming and costly. Machined parts are chosen at random, withdrawn from production, tested, and then the entire batch is validated if the part passes. In the transition of manufacturing, having a faster, smarter, and more reliable means of testing is critical. Embedded meteorology refers to the measurement of items in the manufacturing process that is incorporated into or alongside equipment. Machine shops confront difficulties in adopting these new technologies. You will widen and deepen your competencies and position your business for success in this ever-changing global economy by being an early adopter and embracing change.
Advantages Of Being A Part Of The Smart Manufacturing Environment
When you join an ecosystem, you gain access to innovative skills that can help you transform, as well as the collective wisdom of everyone. Today's producers must produce more relevant, better products at a faster rate to stay competitive. The stakes are high when it comes to leveraging new technologies and tech-savvy individuals to evolve production processes. Given the complexities, most manufacturers do not have these areas completely figured out, despite the fact that their future success is dependent on them. Ecosystems can assist firms accelerate their digital transformation, resulting in near-term growth and long-term strategic benefits. Furthermore, these ecosystems may have a direct impact on financial success.
What Constitutes A Strong Bond?
Ecosystems can produce far more than a slew of new partners or a surge in the number of smart manufacturing use cases. Members of an ecosystem, in their best form—as the example above shows—co innovate around shared challenges, seeking for solutions that benefit more than one player. Within an ecosystem, this is where strong relationships can produce amplified outcomes. Manufacturing respondents that take an external approach to smart manufacturing are more than twice as likely to see benefit in the additional connections or capabilities that their partners contribute. These new connections can provide serendipitous new chances that can help a project move forward faster.
Ecosystem growth can be complicated by challenges and hazards
It's not easy to build an environment for smart manufacturing activities. Many problems could stymie manufacturing companies' attempts to link with a larger network in order to develop their important smart manufacturing goals. Some of the obstacles are related to the hazards of establishing external connections, while others are related to controlling them.
Coordination of ecosystems can be difficult
The coordination effort necessary to operate in tandem with various stakeholders on complicated initiatives over huge manufacturing footprints is an immediate obstacle to deriving benefit from ecosystem interactions. The difficulties they confront in this area were constantly emphasized by executives. When numerous parties are brought together to tackle a problem, there is a risk of "scope creep," which occurs when the project is expanded to make use of the new resources. It's challenging to navigate this issue, especially if a manufacturer doesn't have a lot of experience with technology to ensure interoperability.
Theft Of Intellectual Property Is A Major Concern
The main problem mentioned by surveyed organizations as they manage the possibility of developing external connections to boost smart manufacturing activities is concerns about disclosing IP or smart manufacturing plans. Intellectual property can be particularly difficult to manage in a smart manufacturing setting since it takes on so many different forms.
Skill Sets And Capabilities Differ Depending On The Location Of The Factory
The heterogeneity of numerous firms' footprints was another theme that appeared in the executive interviews. With certain locations embracing digital capabilities more fully than others, implementing a holistic smart manufacturing plan might be difficult. One of the executives interviewed bemoaned the difficulties in achieving a greater level of data maturity that would enable predictive and prescriptive insights for factory-floor production equipment.
Conclusion
Despite the economic downturn, now is not the time to slow down the implementation of smart manufacturing. Rather, the current circumstance appears to be ripe for digital technologies to alleviate many of the issues that manufacturers are facing as they try to keep their businesses running throughout the global pandemic. Companies who are continuing to invest in smart manufacturing in the current market situation are allocating an average of 36% of their global budget for all factory-related projects to smart manufacturing, according to the survey. The ecosystem strategy is effective, but it is difficult to implement. It usually necessitates a concerted effort that includes leadership commitment to smart manufacturing, an organizational strategy, strategic partners chosen to enable or give specific benefits, and continual nurturing of the partnerships and their shared goals.